Choosing the Blade
There are still several remaining scythe factories in the world. In recent years a competitive, market-driven economy is making it difficult for scythe making factories to retain the quality level that was once a standard.
For the farmers in the Global South, the product needs to be affordable, yet fully functional as their livelihood depends on it. Another important aspect is that if the scythe is being introduced to a new region, the new users won’t have the needed skill to compensate for the lack of quality. They might struggle to finish the edge of the blade before receiving the full benefit of what the scythe has to offer.
We started the project with the lower cost blades, thinking this would be a suitable choice for the given circumstances. However, if the blade is not tensioned and tempered adequately, not only does it compromise the performance, but it will have a negative effect on the initial experience and consequently on the whole project.
This led us to select a scythe company willing to collaborate and addresses our particular needs. We were looking for a blade that is out-of-box ready to use with high functionality in the field, uncompromised longevity, but without unnecessary cosmetic finishes, like polishing. We decided to work with one company and focus on one suitable model of the blade, to make it easier for them to have the blades in stock and able to supply even a smaller quantity at a time.
These were our guidelines when choosing a scythe blade supplier. After careful considerations, we’re endorsing the blades supplied by FALCI company of Italy, and using a particular model produced for SWWOB purposes.
Below is the 2019 model produced for the project in India.
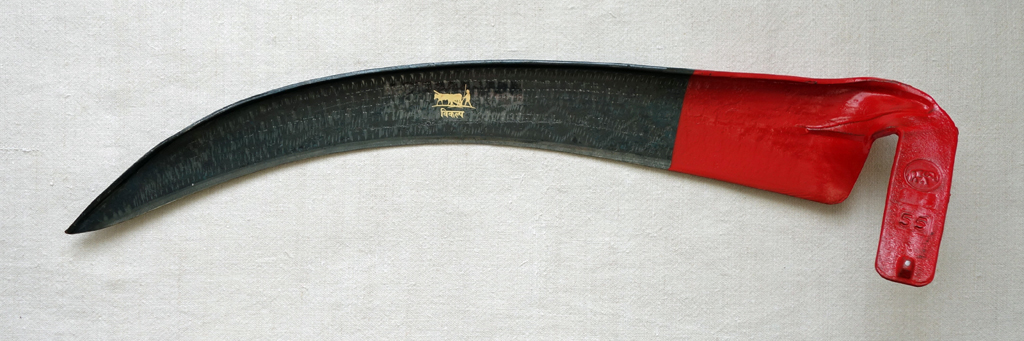
Some thoughts on local blade production
One of the first questions that organizations will as is: “How can we make the blades locally?” This possibility needs a realistic evaluation.
Large-scale blade production requires a major investment in heavy machinery, and specially trained workers to do the job.
Small-scale blade production, by the village blacksmith for example, has its challenges as well. Scythe blades were all forged by local blacksmiths in the distant past, but this required a high level of skill and experience, and it is a very time-consuming process. Out of the half dozen of locally-produced blades that I have witnessed, not one of them has been successfully used in the field. This alternative proves to be more expensive with less control over the quality. If the tool doesn’t meet a satisfactory standard, then the whole project might fail.
From our experience, it is better to instead start with the local production of snaths, cradles, and sharpening accessories which are feasible to produce without a huge investment.